Leading the 'charge' in zero-waste efforts
How Mr Bryan Oh (Business ’19) and Mr Kenneth Palmer (Engineering ’20) are spearheading the recycling of lithium in batteries.
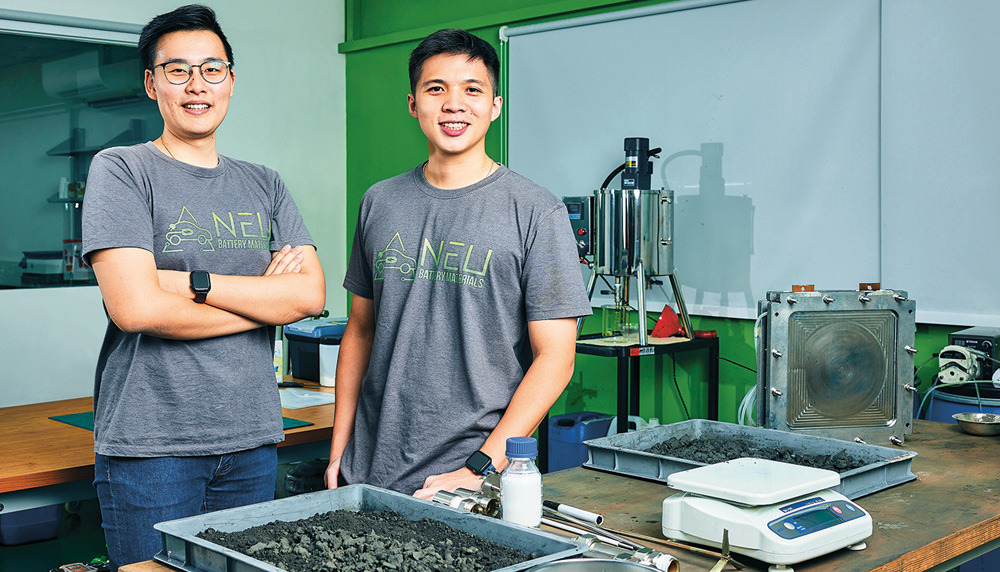
Who They Are
To Mr Bryan Oh and Mr Kenneth Palmer, the best way to make an impact for a cause you care about is to do it yourself as an entrepreneur. The pair — who met as undergraduates at NUS — are the co-founders of lithium battery recycling company NEU Battery Materials, which has commercialised the technology to recycle lithium from used batteries. This potentially reduces the need for lithium mining, which has an adverse impact on the environment.
Roads worldwide are becoming much greener thanks to the growing adoption of electric vehicles (EVs). These rides — which are quieter and thus also reduce noise pollution — have been championed as a way of cutting carbon emissions. But EVs bring their own set of problems: What should be done with the battery waste they generate?
EVs put on the road, in 2019 alone, produced 500,000 tonnes of battery waste, according to Eco-Business. Most of these batteries’ components are currently recycled, but a key one — lithium — is generally not. Lithium is often left out of the recycling process because extracting it and then purifying it for reuse is extremely complicated and expensive. Without an alternative, most battery manufacturers end up mining more lithium instead of recycling the lithium from batteries. This spells doom for sustainability efforts, as mining lithium has been shown to harm the environment in many ways. For instance, it is a tremendously resource-intensive process: approximately 2.2 million litres of water is needed to produce one tonne of lithium. And extracting that amount of lithium from the earth puts 15 tonnes of carbon dioxide into the air.
The problems of lithium mining may not be apparent where we are from, but we will certainly see the effects of battery waste as the number of EVs plying our roads grows.
Mr Kenneth Palmer
Enter NEU Battery Materials, a startup making waves in the recycling space by championing the use of electricity to extract lithium from used batteries, specifically those known as Lithium Iron Phosphate (LFP) batteries. This technology, which was first developed at the University in 2017, has a positive impact on the environment as it reduces the amount of water and chemicals needed to extract lithium. Its co-founders, Mr Bryan Oh, 28, and Mr Kenneth Palmer, 27, who met at the University, are driven by a passion for sustainability. “We hope that beyond making an impact on recycling in the EV industry, we can also educate the wider community on recycling,” Mr Oh explains. “In absolute terms, waste generated in Singapore is smaller than in larger countries. But we want to help build a country where the waste that goes to our landfill is minimised.”
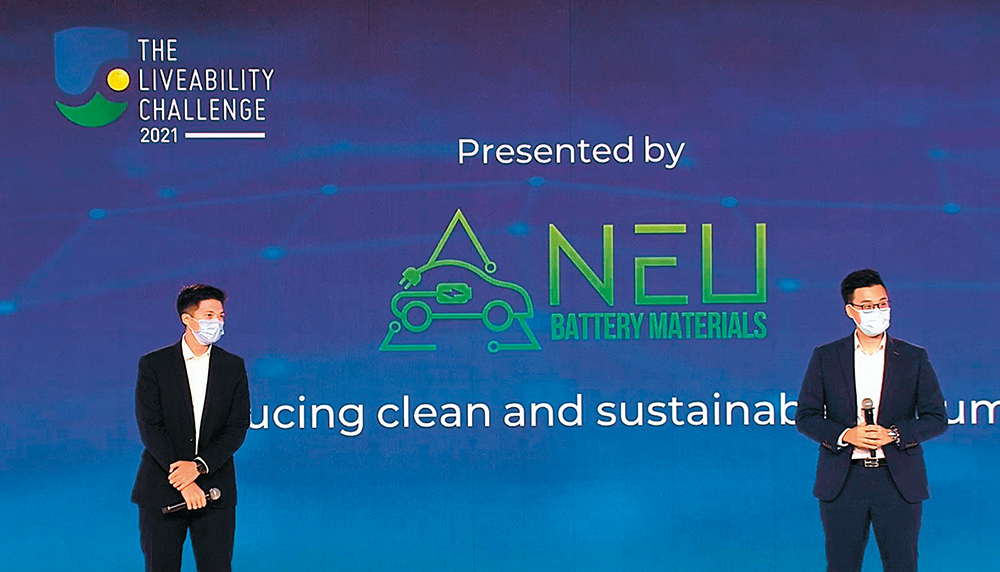
How did you learn about lithium recycling technology?
Bryan Oh (BO): We learnt about the lithium mining process and how this new technology could recycle lithium, at GRIP MAKE, an initiative by the NUS Graduate Research Innovation Programme (GRIP). GRIP MAKE enables fresh NUS graduates to develop commercially viable ideas based on the University’s intellectual property. It builds on the GRIP programme, which helps researchers and postgraduate students to commercialise their technologies on their own or through partnerships with other NUS students and alumni.
Why were you keen to take up the challenge of commercialising it?
BO: Recycling has to be done right, and it has to be financially viable. Otherwise, it is not sustainable in the long term. We believe that entrepreneurship is the best way to tackle issues like these and were keen to take up the challenge of making lithium battery recycling a profitable venture for all parties involved.
Kenneth Palmer (KP): If we had to sum it up, our goal with NEU Battery Materials is to make the process of lithium extraction cleaner, less polluting, more efficient in terms of scaling up and, ultimately, more affordable. We want lithium recycling to be a sustainable endeavour.
Has it been challenging to convince businesses to use NEU Battery Materials' technology?
KP: In some ways, it is a challenge because we recycle a specific kind of battery that nobody is currently recycling. So we do have to demonstrate to businesses that our technology is the solution they have been looking for. But on the other hand, it is also easier to convince businesses because they have been hankering for a solution like this.
BO: You can also get a sense of the industry’s readiness for a solution like this from the funding and support we have received from partners like Temasek Foundation, which gave us a grant to pilot our solution. Once that was successful, we expanded to have our own battery recycling facility in Jurong alongside our R&D lab in Bukit Batok.
What are your plans for NEU Battery Materials?
BO: We envision that one day, if you see a battery manufacturing facility — be it in China, Europe or the United States — you’ll see a NEU Battery Materials recycling plant nearby to help service the end-of-life management of these batteries. On this front, partnerships are extremely valuable. It is impossible to service the entire world alone. So, the partnerships we forge with battery manufacturers and lithium users will be valuable.
KP: Being a homegrown company, we also want to support the recycling of all batteries in Singapore. The problems of lithium mining may not be apparent where we are from, but we will certainly see the effects of battery waste as the number of EVs plying our roads grows.
Green is the goal
Ask Mr Oh and Mr Palmer what their goal is for a greener Singapore, and they say in unison, “A circular economy mentality”. Explains Mr Oh, “This means that we must adopt the mindset of making things last longer and finding ways to reuse what we already have.”
To Mr Palmer, this also means shaking off the mindset that a device or tech tool needs to be upgraded every time there is a new version out. “But if you do have to upgrade, please dispose of your used electronics properly by leaving them at e-waste collection points,” he says. “Simple acts like that go a long way towards preserving resources.”
This article first appeared in the Apr-Jun 2023 issue of the Alumnus magazine.